Our Company
Shanghai 4New Control Co., Ltd. specializes in research and development of oil and liquid cooling and filtering, cutting fluid purification and regeneration, oil and scum removal, oil-water separation, oil-mist collection, chip dehydration, efficient transportation of chip dirty liquid, waste chip pressing, gas mist condensation and recovery, oil precise temperature control and other equipment for various equipment and production line; Design and manufacture various cutting fluid centralized filtration systems, special and high-precision filtering and temperature control devices and test equipment for users, and provide supporting filtering materials and filtering and temperature control technical services.
30+ years of operating experience, leading product design and technical services gradually cover the entire field of metal cutting processing; R&D and production are developing steadily; The technical capabilities will be comparable to world-class enterprises and will move from domestic to international; 4New has passed the ISO9001/CE certificates and has scored several patents and awards; Create value for customers, coexist and win-win with employees; Help transform traditional processing and manufacturing into advanced manufacturing.
Hundreds of famous enterprises at home and abroad, including GM in the United States and Landis in the United Kingdom, Junker in Germany and Schleiffing Machine Tool Group in Germany, Shanghai General Motors, Shanghai Volkswagen, Changchun FAW Volkswagen, Dongfeng Motor Engine, DPCA, Grundfos Water Pump, SKF Bearing, etc., have selected our products as their supporting facilities.
Organizational Structure
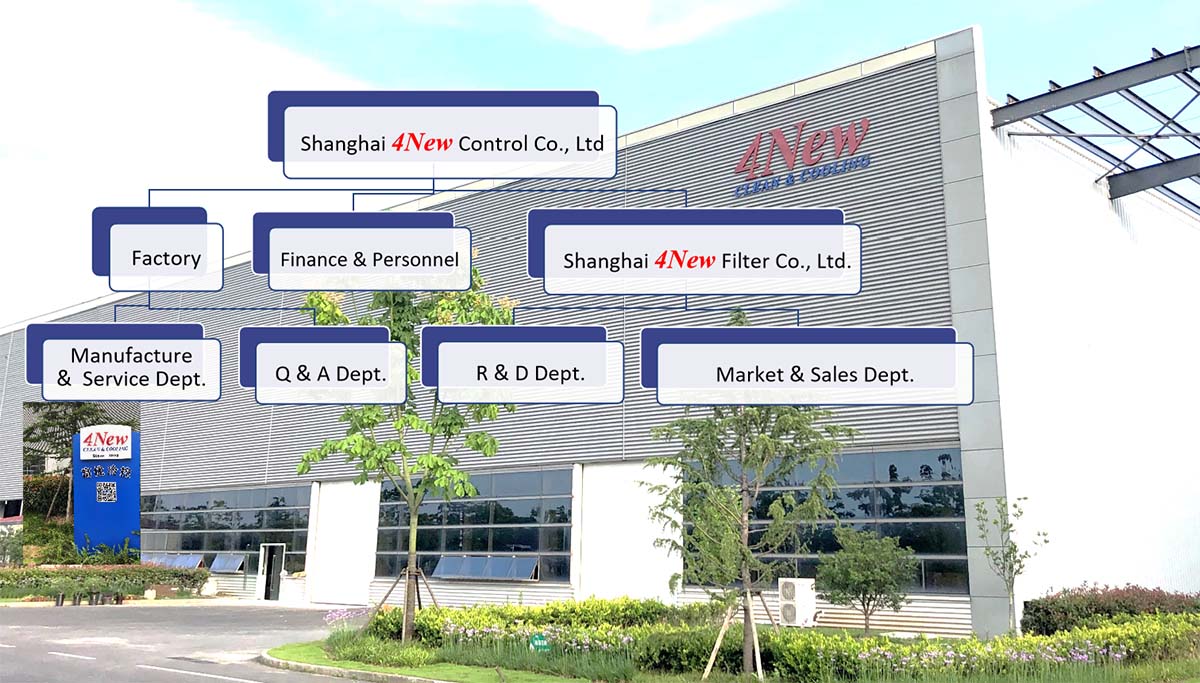
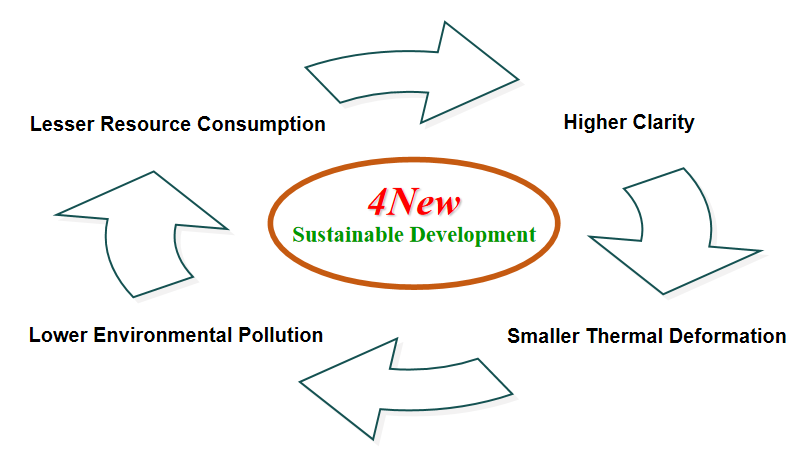
Business Concept
4New takes the mission of "green processing" and "circular economy" as the company's mission to constantly develop and innovate consumable free filtering, and strives to make progress towards the ideal goal of "Higher Clarity, Smaller Thermal Deformation, Lower Environmental Pollution, and Lesser Resource Consumption" in green manufacturing. Because it conforms to the development direction of human society and is the only way for the sustainable development of manufacturing industry, it is also the way for 4New's sustainable development.
Exhibition
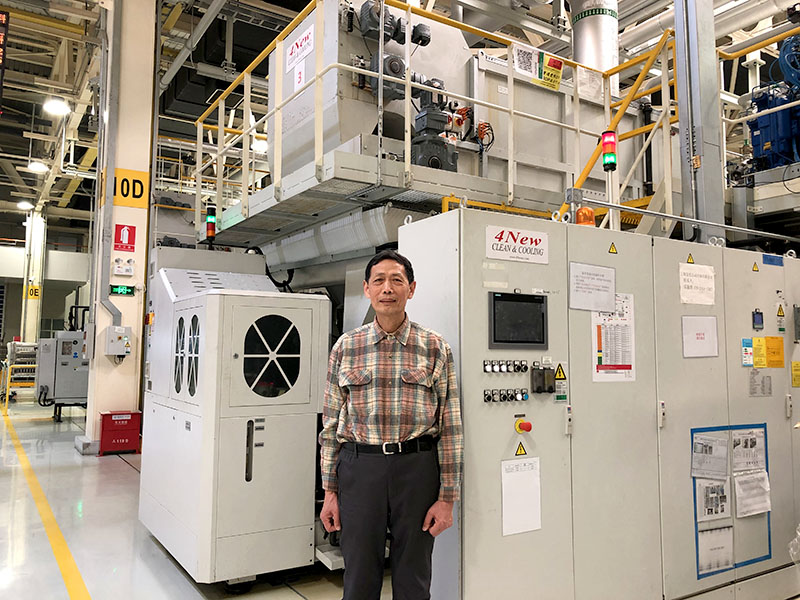
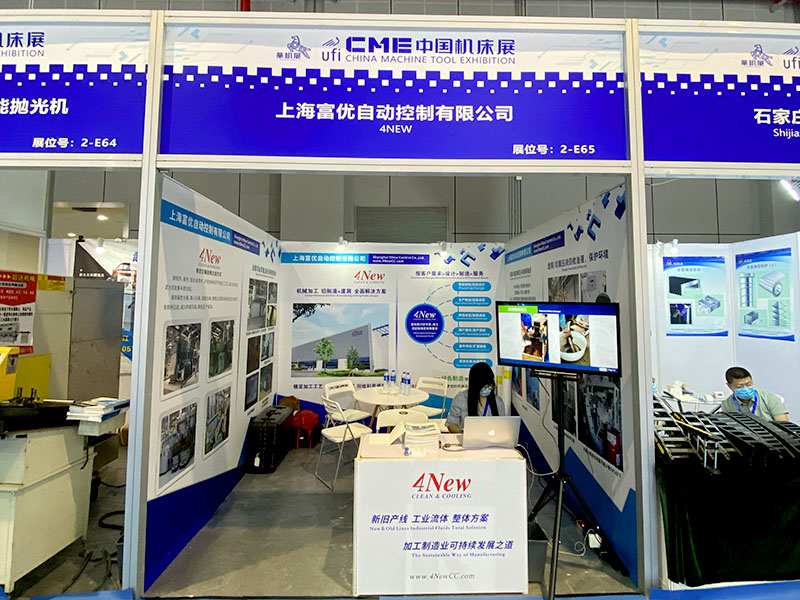
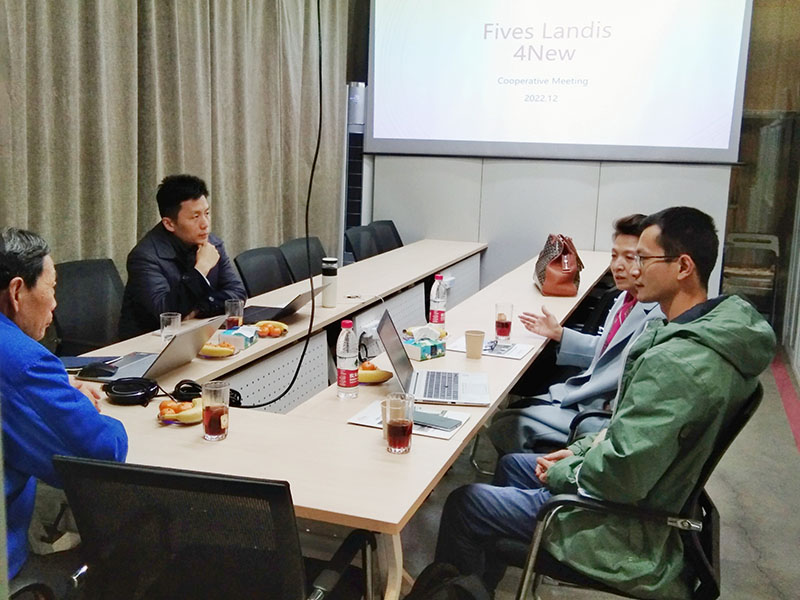
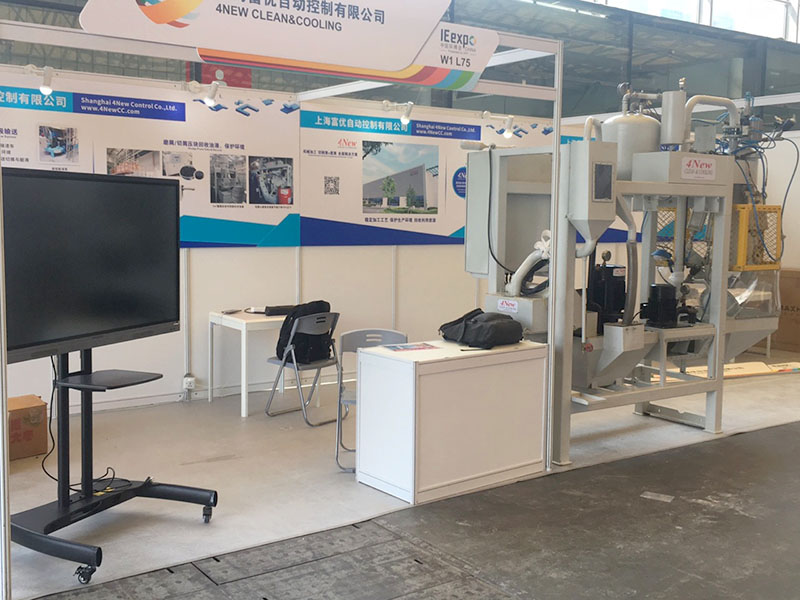
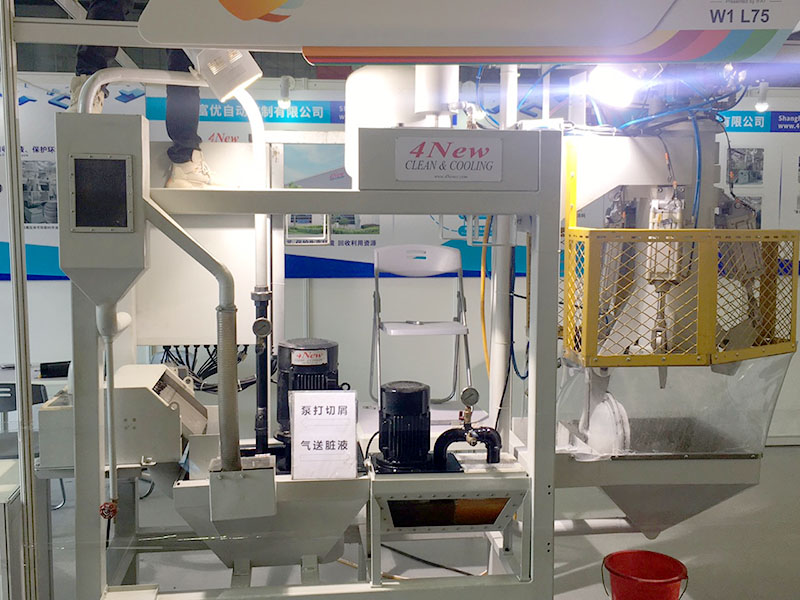
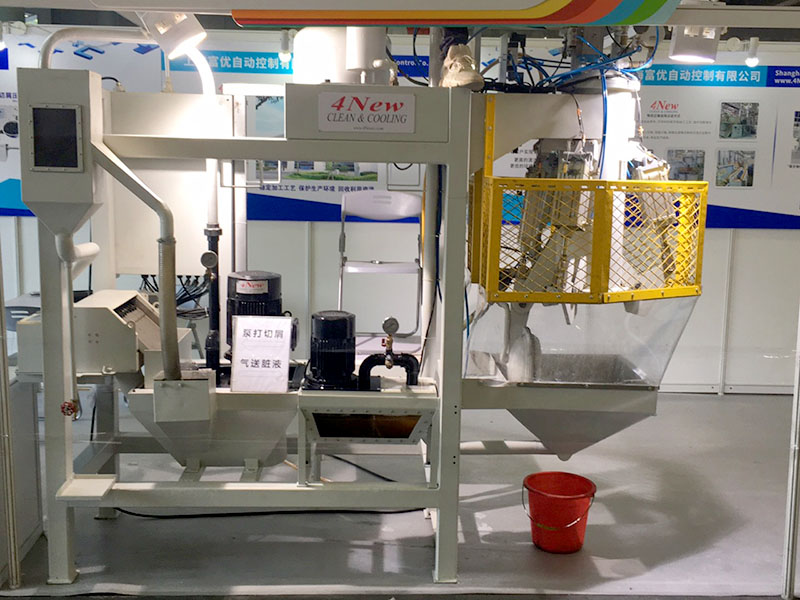
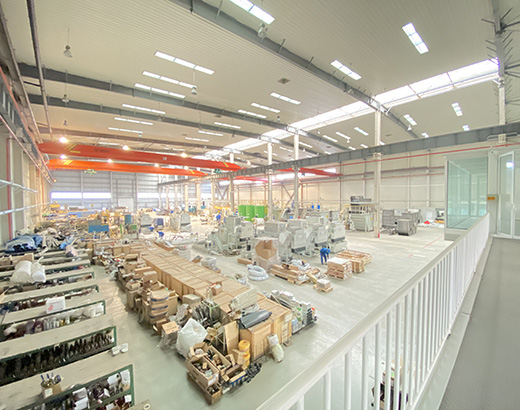
Professional Services
4New has a complete service system and a professional service team with rich professional knowledge and on-site service experience to provide users with one-stop services from product selection to installation and commissioning. Over 30 years, 4New has provided hundreds of users in machine tool industry, automobile industry and other industries at home and abroad with various cooling temperature control, filtering and purification devices with excellent performance, so that users can enjoy the best products and services at the lower cost.
Production Equipment
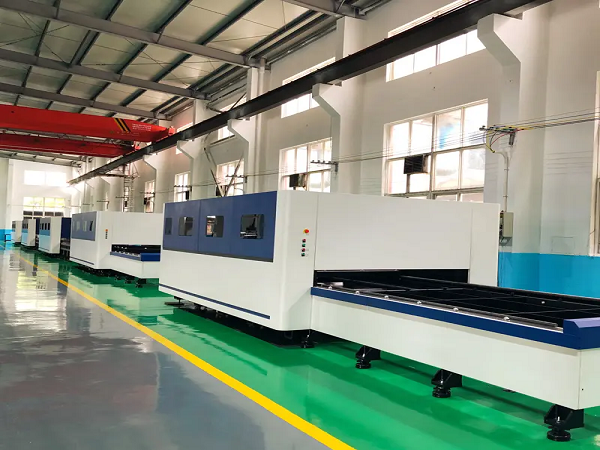
Laser cutting machine
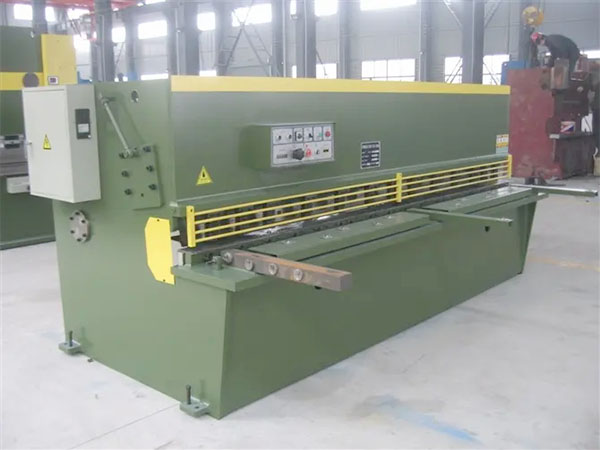
Shearing machine
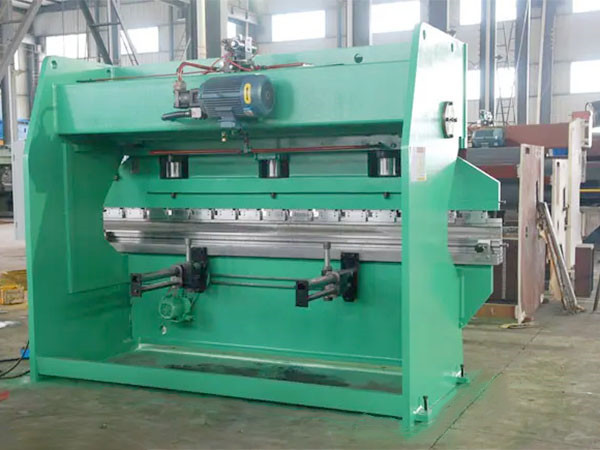
Bending machine
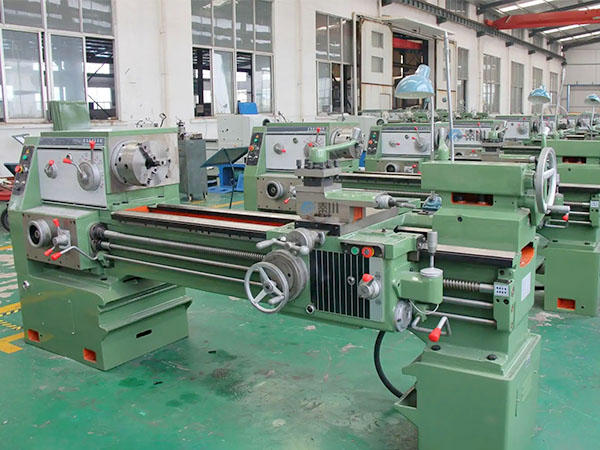
Lathe
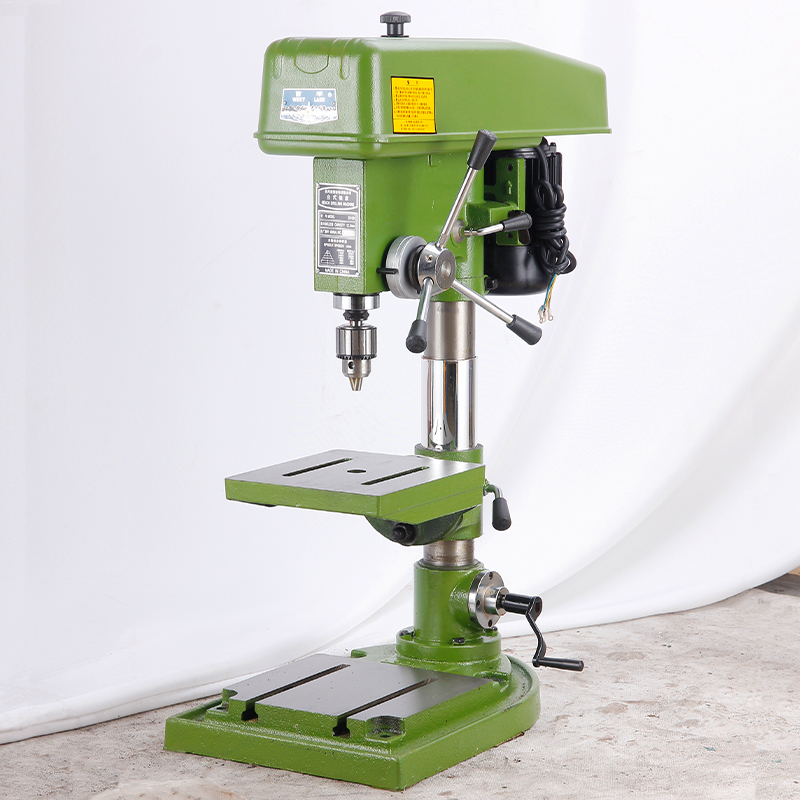
Bench drill
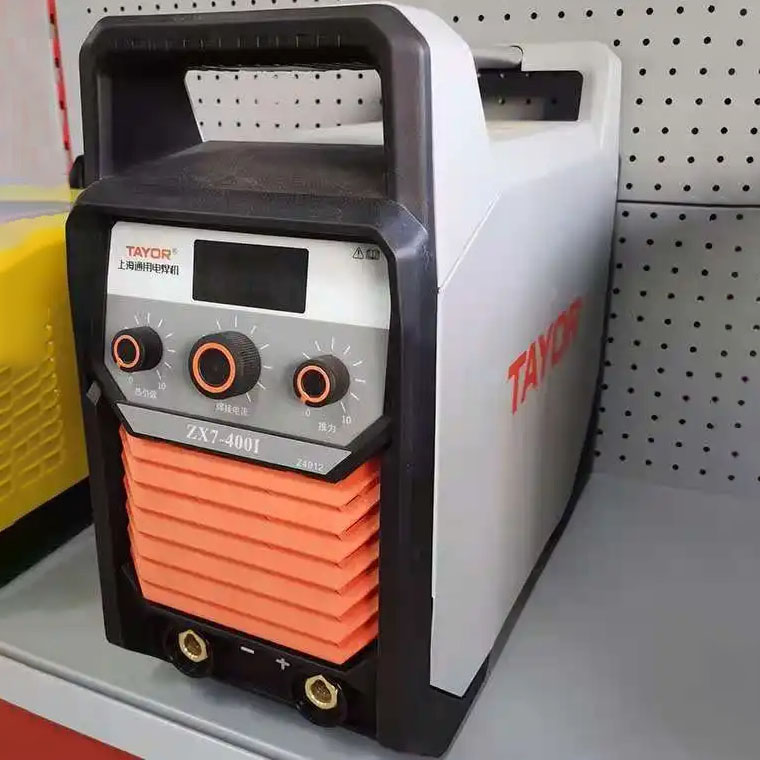
Plasma cutting machine
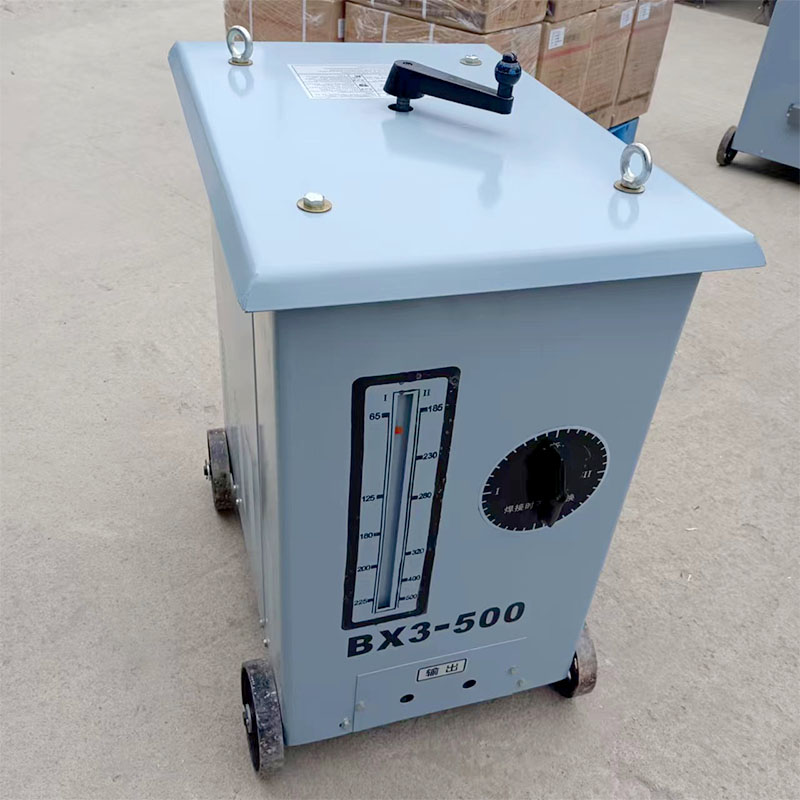
Electric welding machine

Threading machine
Background of 4New Company
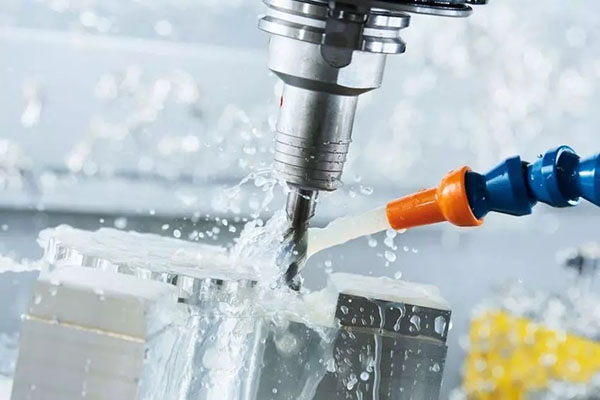
As we know, metal cutting will generate a lot of heat to wear tools and deform workpieces. It is necessary to use coolant to quickly take away the processing heat and control the processing temperature. However, the strong friction between the impurities in the coolant and the tool and workpiece will deteriorate the quality of the machined surface, shorten the tool life, and also produce a lot of oil mist to pollute the air, waste liquid and slag to damage the environment.
Therefore, improving the cleanliness of cutting fluid and controlling the temperature of cutting fluid can reduce tolerance dispersion, reduce waste products, improve tool durability and effectively improve machining quality.
In addition, the precision temperature control technology can also be used to precisely control the thermal deformation of parts to improve the machining accuracy. For example, controlling the temperature change of the reference gear of the gear grinder within ± 0.5 ℃ can realize the gapless transmission and eliminate the transmission error; The screw pitch error can be controlled with micrometer accuracy by adjusting the screw processing temperature with 0.1 ℃ accuracy. Obviously, precision temperature control can help machining achieve high-precision machining that can not be achieved by mechanical, electrical, hydraulic and other technologies alone.
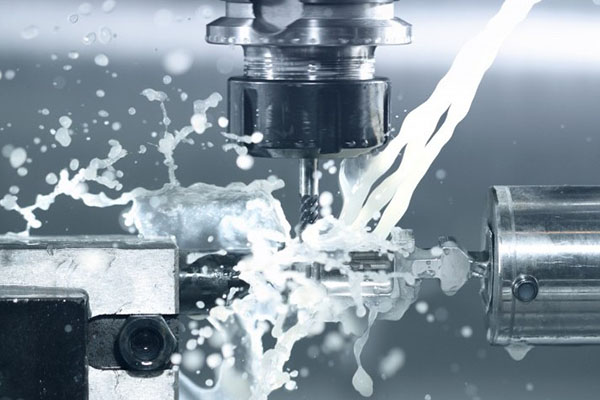