Cutting fluid is an industrial fluid used to cool and lubricate tools and workpieces during metal cutting and grinding.
Type of cutting fluids
Water based cutting fluid can be divided into emulsion, semi synthetic cutting fluid and fully synthetic cutting fluid. The diluent of emulsion is milky white in appearance; The diluent of semi synthetic solution is usually translucent, and some products are milky white; The diluent of synthetic solution is usually completely transparent, such as water or slightly colored.
Function of cutting fluids
1. Lubrication
The lubricating effect of metal cutting fluid in the cutting process can reduce the friction between the rake face and chips, and between the back face and the machined surface, forming a partial lubricating film, thus reducing the cutting force, friction and power consumption, reducing the surface temperature and tool wear of the friction part between the tool and the workpiece blank, and improving the cutting performance of the workpiece material.
2. Cooling
The cooling effect of cutting fluid is to take the cutting heat away from the tool and workpiece through the convection and vaporization between it and the tool, chip and workpiece heated by cutting, so as to effectively reduce the cutting temperature, reduce the thermal deformation of workpiece and tool, maintain the tool hardness, and improve the machining accuracy and tool durability.
3. Cleaning
In the process of metal cutting, cutting fluid is required to have a good cleaning effect. Remove the generated chips, abrasive chips, iron powder, oil dirt and sand particles, prevent the contamination of machine tools, workpieces and tools, and keep the cutting edge of tools or grinding wheels sharp without affecting the cutting effect.
4. Rust prevention
In the process of metal cutting, the workpiece will be corroded by contacting with corrosive media such as oil sludge generated by decomposition or oxidative modification of environmental media and cutting fluid components, and the surface of machine tool components contacting with cutting fluid will also be corroded.
Extended data
Differences between different cutting fluids
The oil base cutting fluid has good lubrication performance and poor cooling effect. Compared with oil-based cutting fluid, water-based cutting fluid has poorer lubrication performance and better cooling effect. Slow cutting requires strong lubricity of cutting fluid. Generally speaking, cutting oil is used when the cutting speed is lower than 30m/min.
Cutting oil containing extreme pressure additive is effective for cutting any material when the cutting speed does not exceed 60m/min. During high-speed cutting, due to the large heat generation and poor heat transfer effect of oil-based cutting fluid, the temperature in the cutting area will be too high, which will lead to smoke, fire and other phenomena in the cutting oil. In addition, because the workpiece temperature is too high, thermal deformation will occur, which will affect the machining accuracy of the workpiece, so water-based cutting fluid is used more.
Emulsion combines the lubricity and rust resistance of oil with the excellent cooling property of water, and has good lubricity and cooling property, so it is very effective for metal cutting with high speed and low pressure generated by a large amount of heat. Compared with oil-based cutting fluid, the advantages of emulsion lie in its greater heat dissipation, cleanability, and economy due to dilution with water.
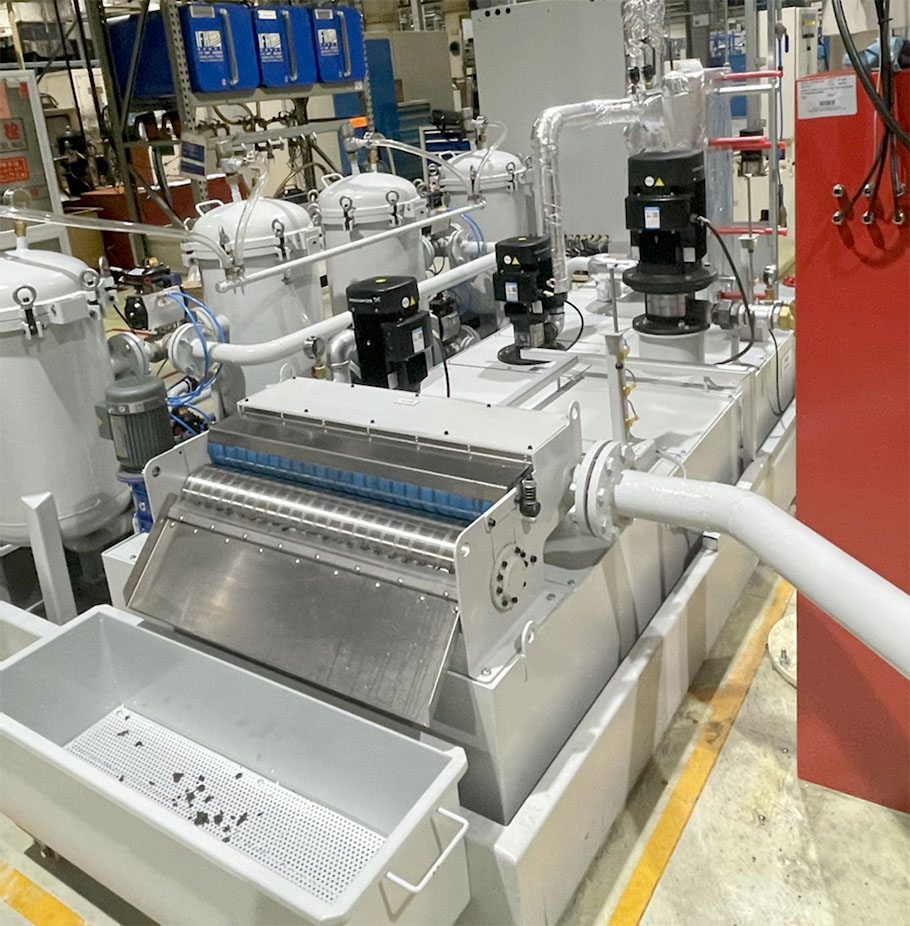
Post time: Nov-03-2022